I already have an article about a specific type of HID device called
trackballs, so I decided to make the picture complete and do a much bigger and ambitious one about mechanical keyboards.
For now, we will talk rather more about types and variations instead of particular keyboards. So here we go: numerous customization routes.
Switches
Let's start from the switch's classification.
Anatomy and Profile
The standard mechanical switch profile was not changed significantly for many years. Just look at the patent explosion scheme from 1984.
(from original patent
4,467,160)
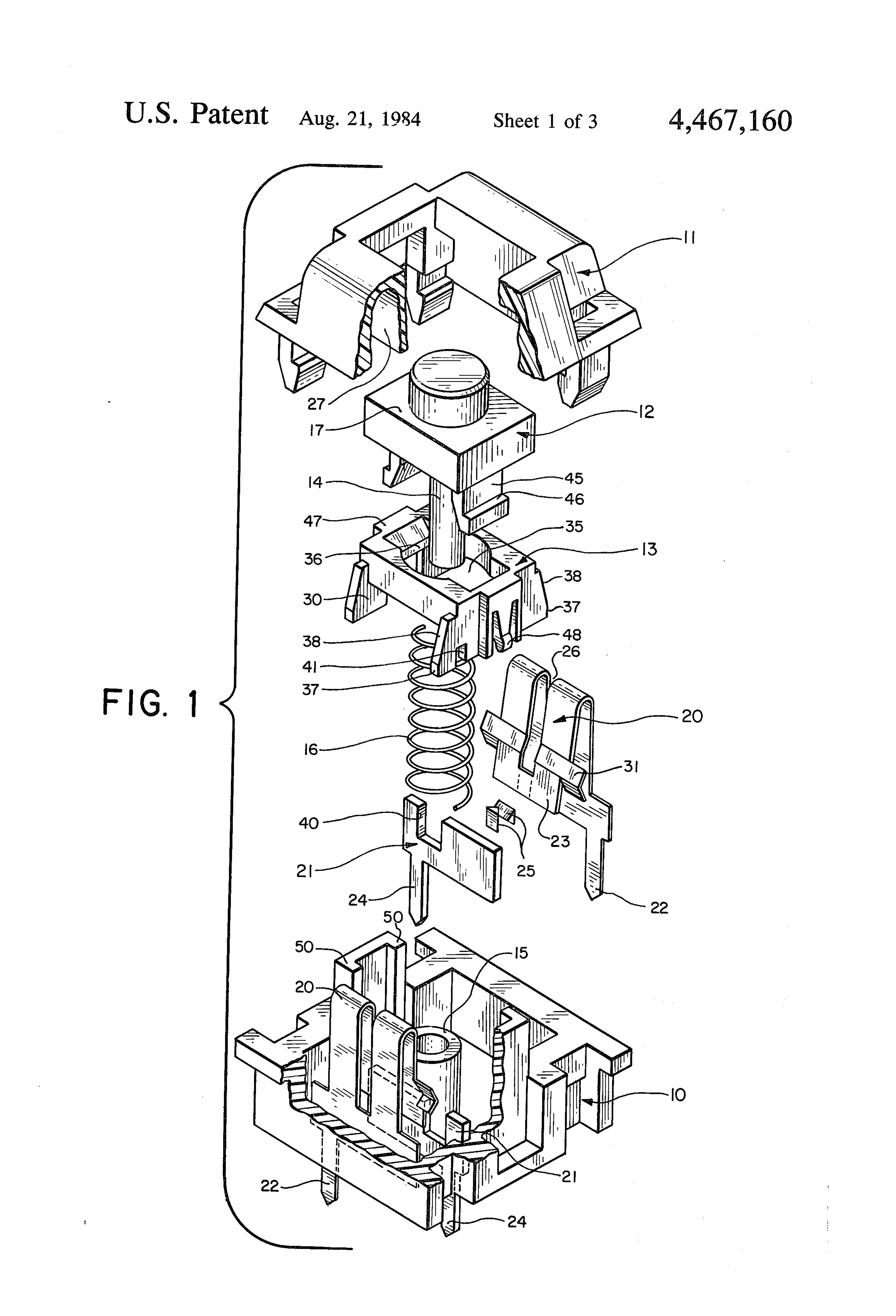
As a reference, I am going to use the most common electrical transferring switch with linear moving mechanism as the closest in design to its ancestor and the simplest in terms of operation. It will be the base that will grow with additional details along this guide. Here is the list of parts:
1 - top housing - top part of the switch housing.
2 - bottom housing - bottom part of the switch housing.
3 - stem - main movable part of the switch.
4 - leaves - two metal contact elements inside switch.
5 - spring - for pushing movable part back.
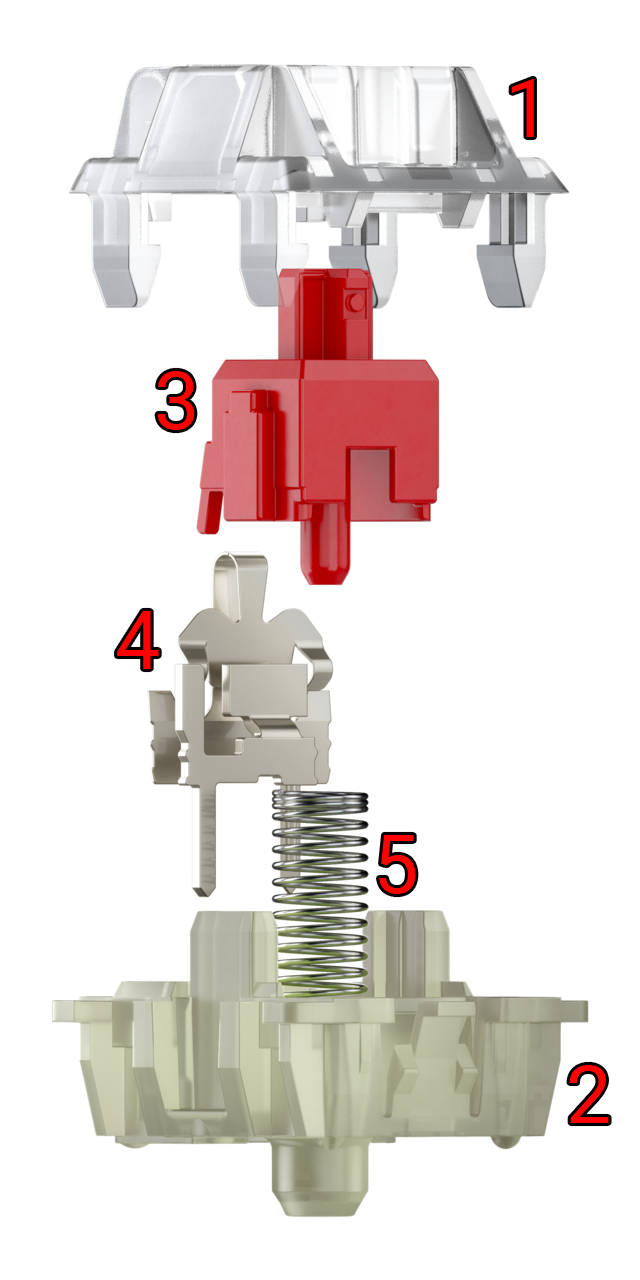
Top housing:
1 - stem slot
2 - LED slot
3 - clips
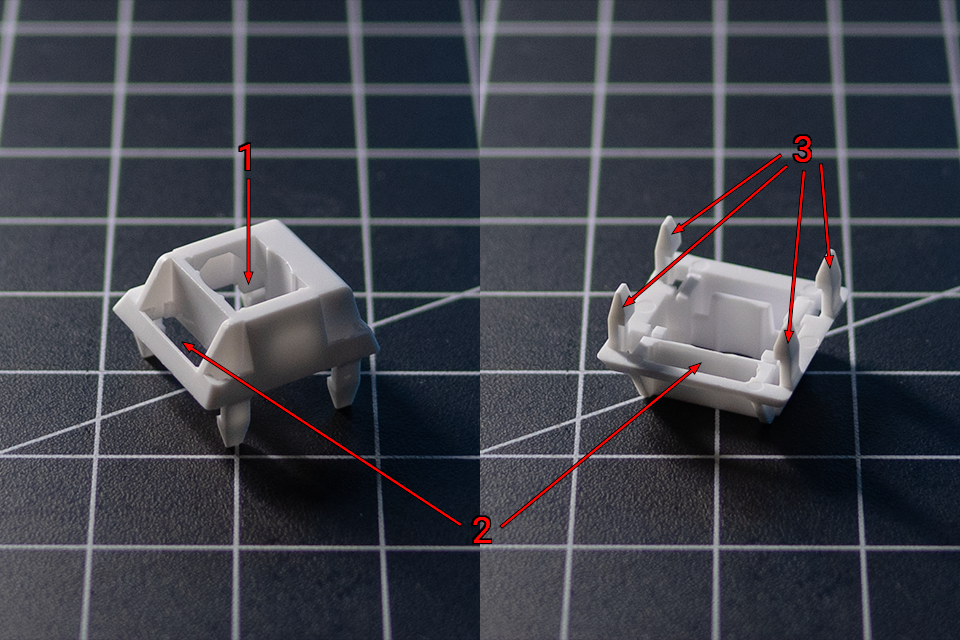
Bottom housing:
1 - center mast
2 - rails
3 - leaves sockets
4 - leaves pin holes
5 - LED slot
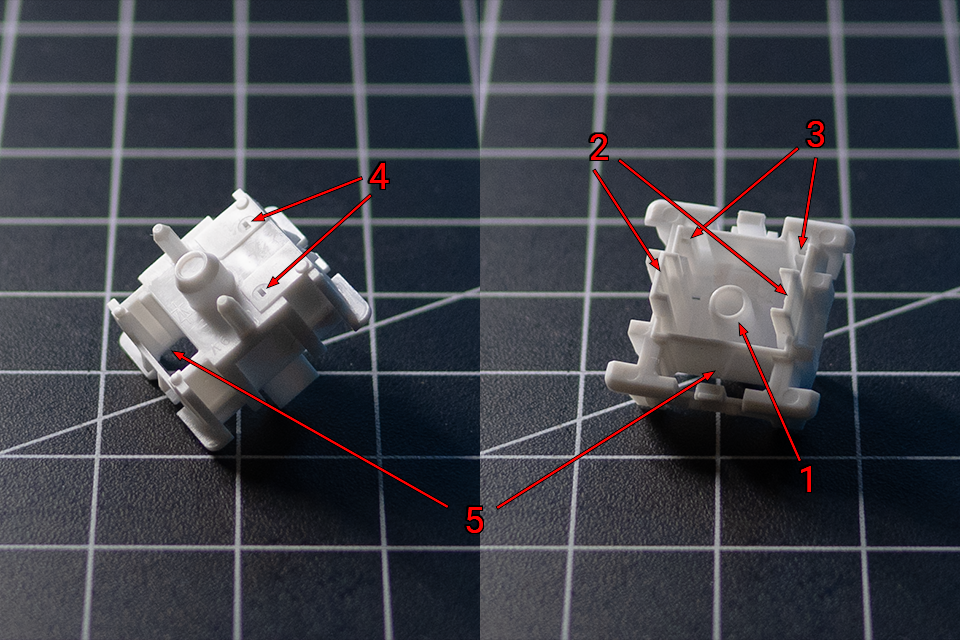
Stem:
1 - front face
2 - back face
3 - legs
4 - rails
5 - center pole
6 - keycap mount
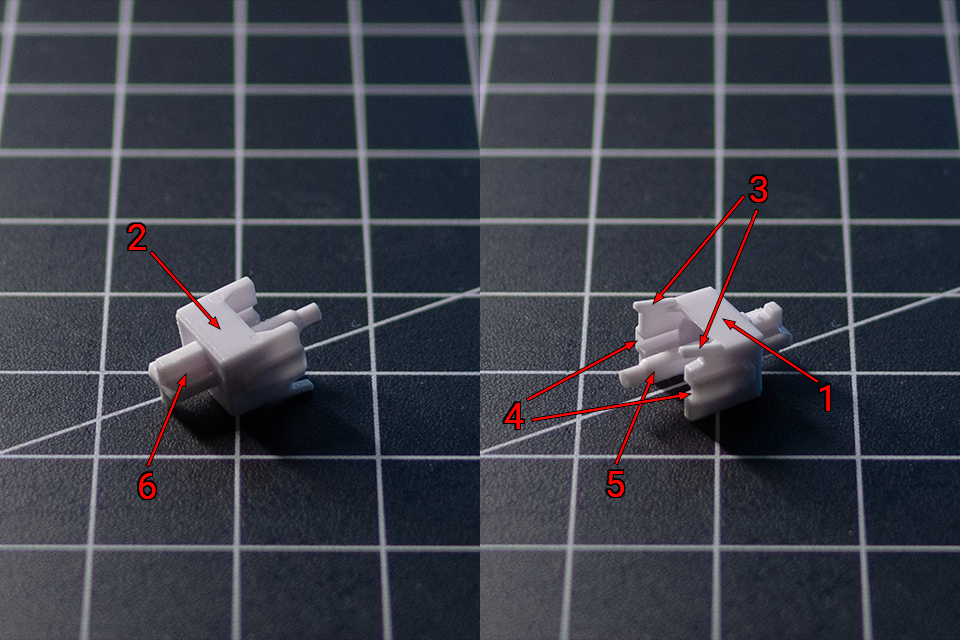
Leaves:
1 - dynamic leaf
2 - static leaf
3 - pins
4 - contact points
5 - arms
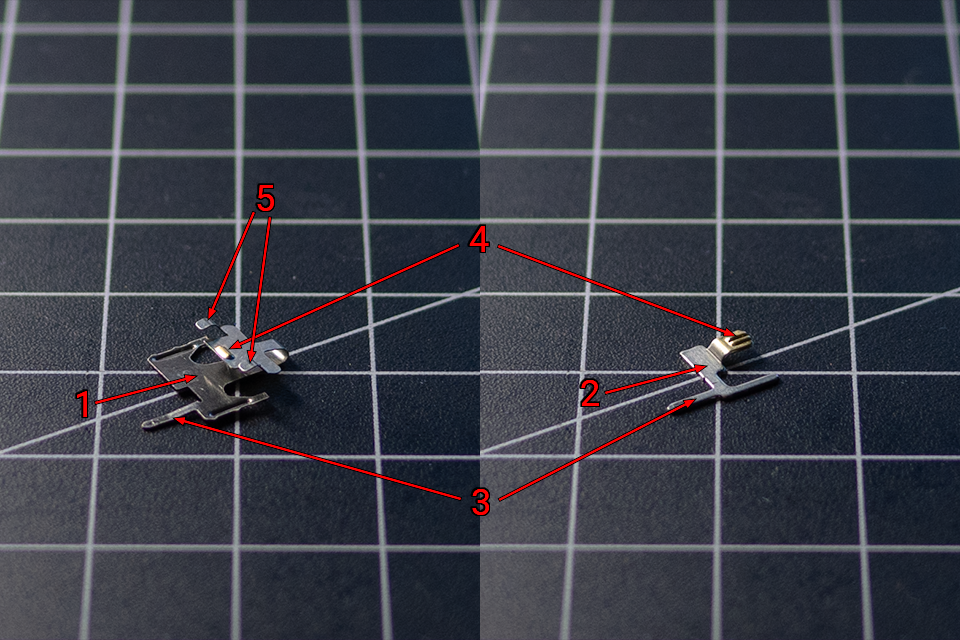
Spring:
It is just a spring.
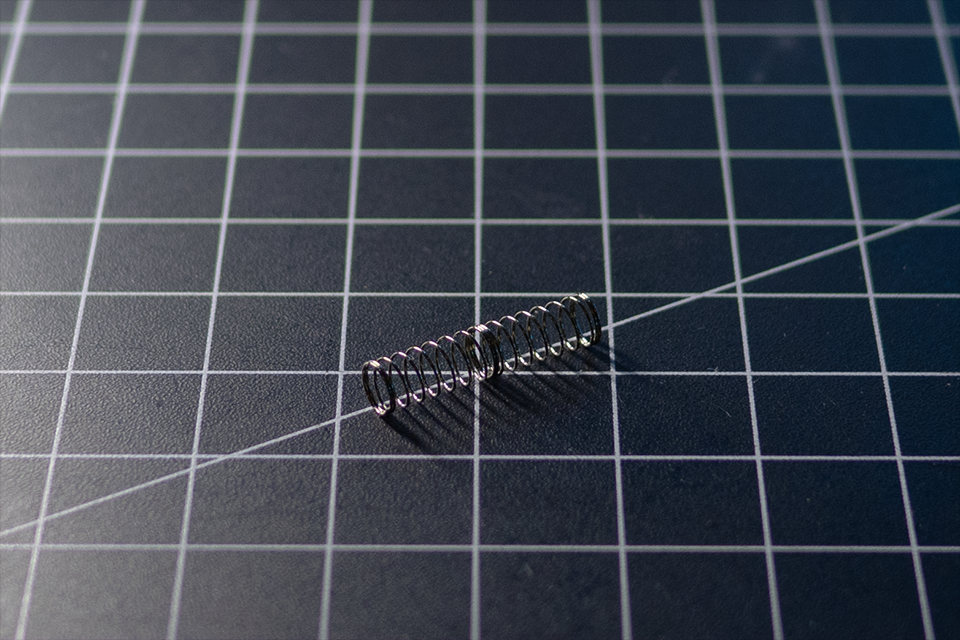
And now you know the basic naming of the parts and parts of the parts. For some, there are no official names, so I simply use the most appropriate ones, or those that are more commonly used in the community.
Product design runs in circles. Just as once large industrial mechanical keyboards were replaced by thin membrane ones, so some time after the rebirth of mechanical keyboards, the demand for something more compact has reappeared. Various companies began to experiment in attempts to stuff the classic mechanism into something more compact in height. This is how low-profile switches appeared on the market. They have a similar classification to the classic profile, but in terms of compatibility, everything is complicated. The basic idea of custom mechanical keyboards was to make all parts cross-compatible between builds, and the classic profile fully corresponds to this ideology. However, for low-profile everybody just decides to head their own way, and it causes... oh boy... this.
(photo by
Pavlo Khmel)
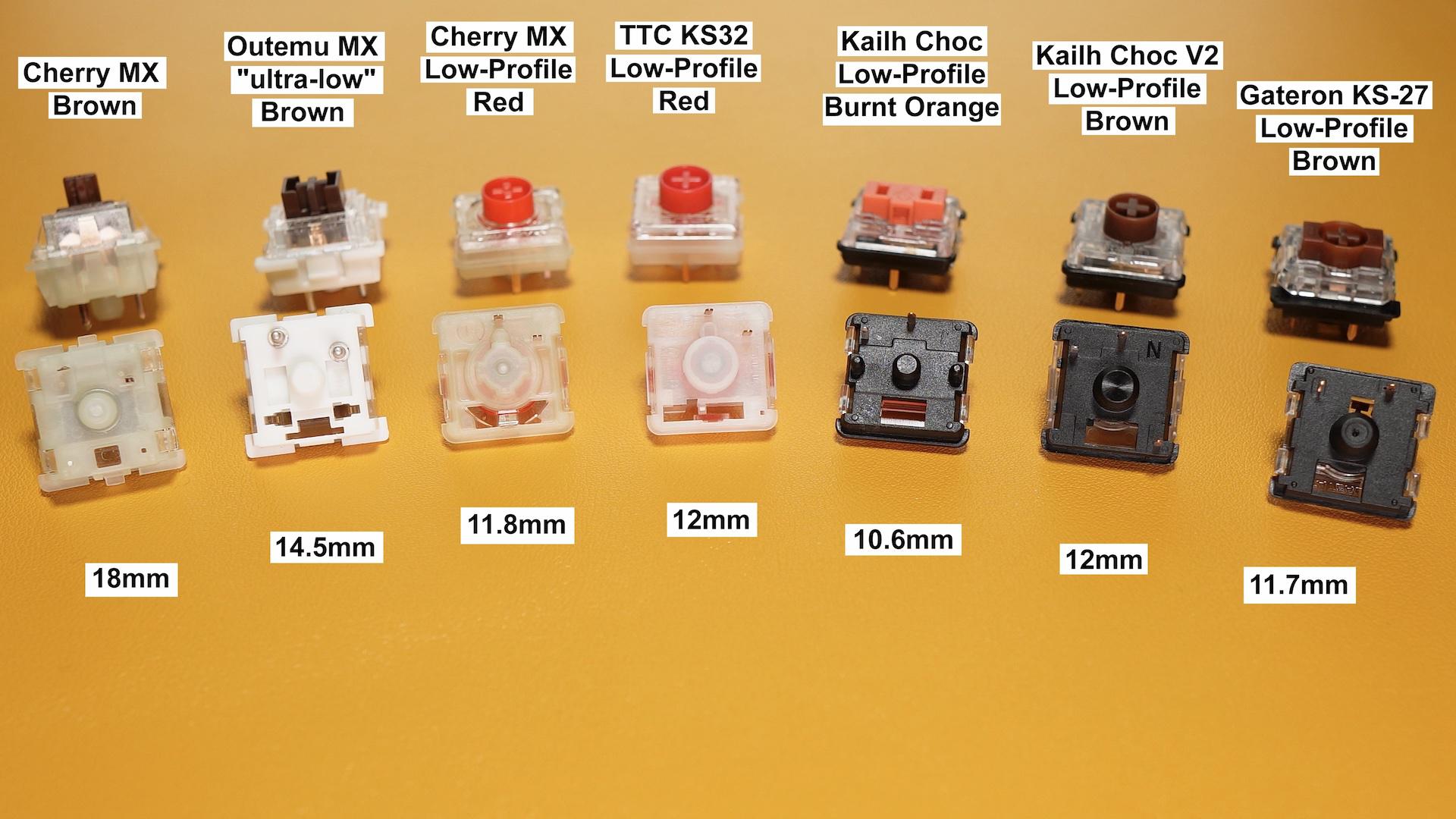
Signal transferring
Electrical
This is the most common switch type where two metal leaves inside are taking part of the contact elements.
Each leaf has a pin part that sticks outside the plastic body and makes each switch of this type a self-sufficient electrical component that is located off the board. By default, stem legs are pushing out dynamic leaf arms. Therefore, the contact point of the dynamic leaf pushed out of the contact point of the static leaf as well, and they are not touching each other. When the switch is pressed, the stem goes down and dynamic leaf arms glide over the slop of the stem legs, so eventually contact points of the leaves touch each other. The electrical circuit is closed, and the key is considered actuated.
Optical
This is an experimental switch type with the idea of reducing response time by using for actuation light instead of electricity.
In this case, dynamic leaf is placed only in tactile and click types of switches and only for the sake of changing the tactile characteristics with leaf arms and stem legs interaction. It is not taking part in an electrical circuit. Instead, for each switch, we have pairs of infrared light emitters and receivers on the circuit board, one opposite to another. Construction of the bottom housing center mast allows passing this light through, and the center pole of the stem plays a role of a shutter. When the switch is pressed, the stem goes down, and the center mast blocks light flow from the emitter to the receiver. The signal breaks, and the key is considered actuated.
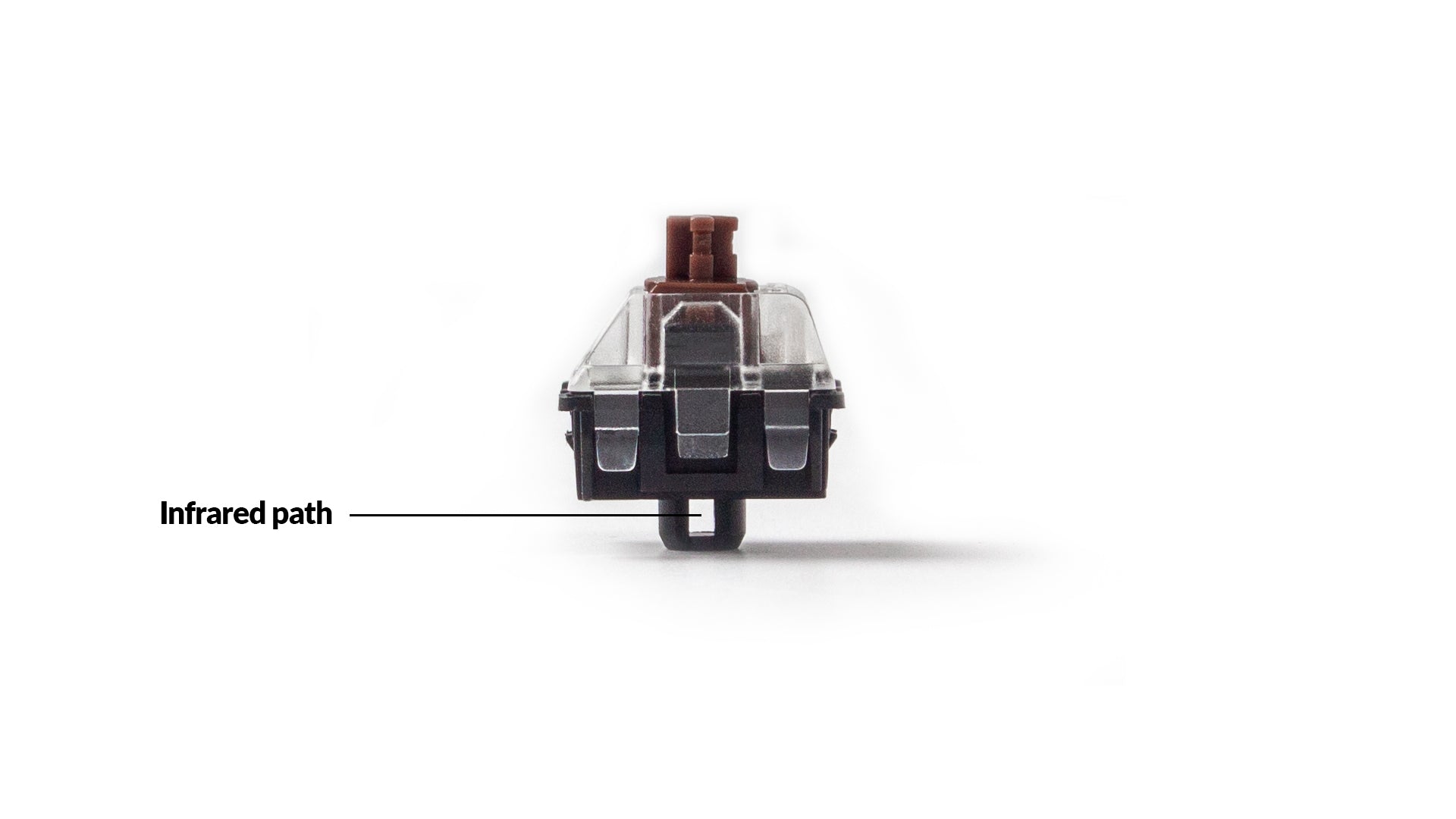
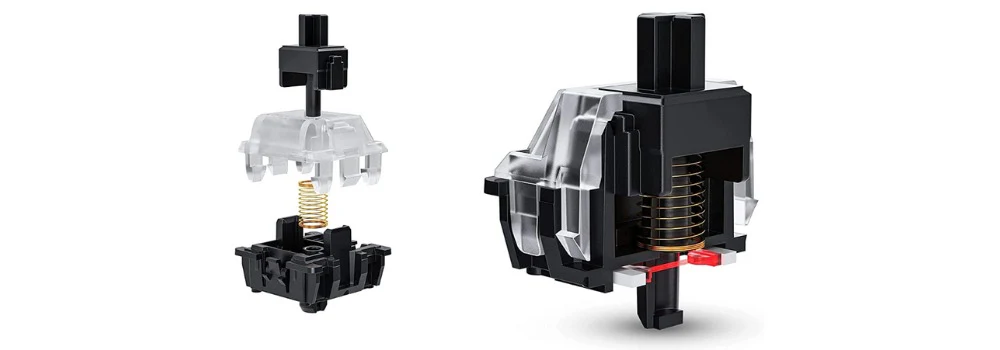
Electromagnetic
This is a relatively new and gaining its popularity switch type, which is based on the Hall effect.
The same as for the optical one, these types of switches are not playing a direct role in the electrical circuit. For each switch, there is a magnet integrated in the bottom of the stem center pole. And for each switch, there is a Hall sensor located on the circuit board. When the switch is pressed, the stem goes down, so the magnet on the center pole gets closer to the Hall sensor and changes readings of the electromagnetic field. In this case, the software part does not operate with binary values but receives data about how deeply the key is pressed. This opens the possibility not only to tweak the depth of the switch actuation, but also to bind different macros or logic to different pressure depths of each switch.
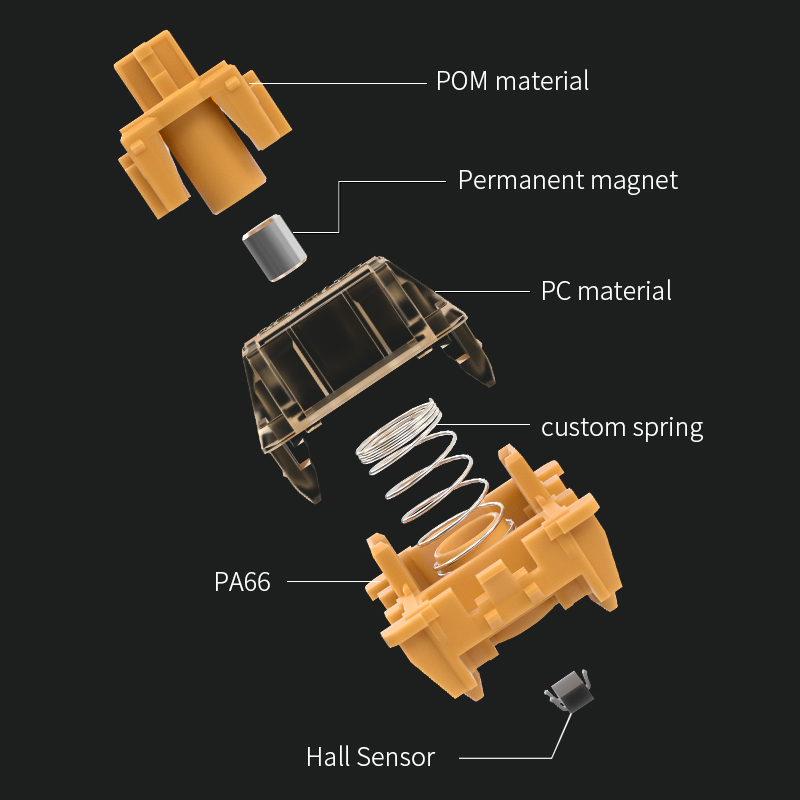
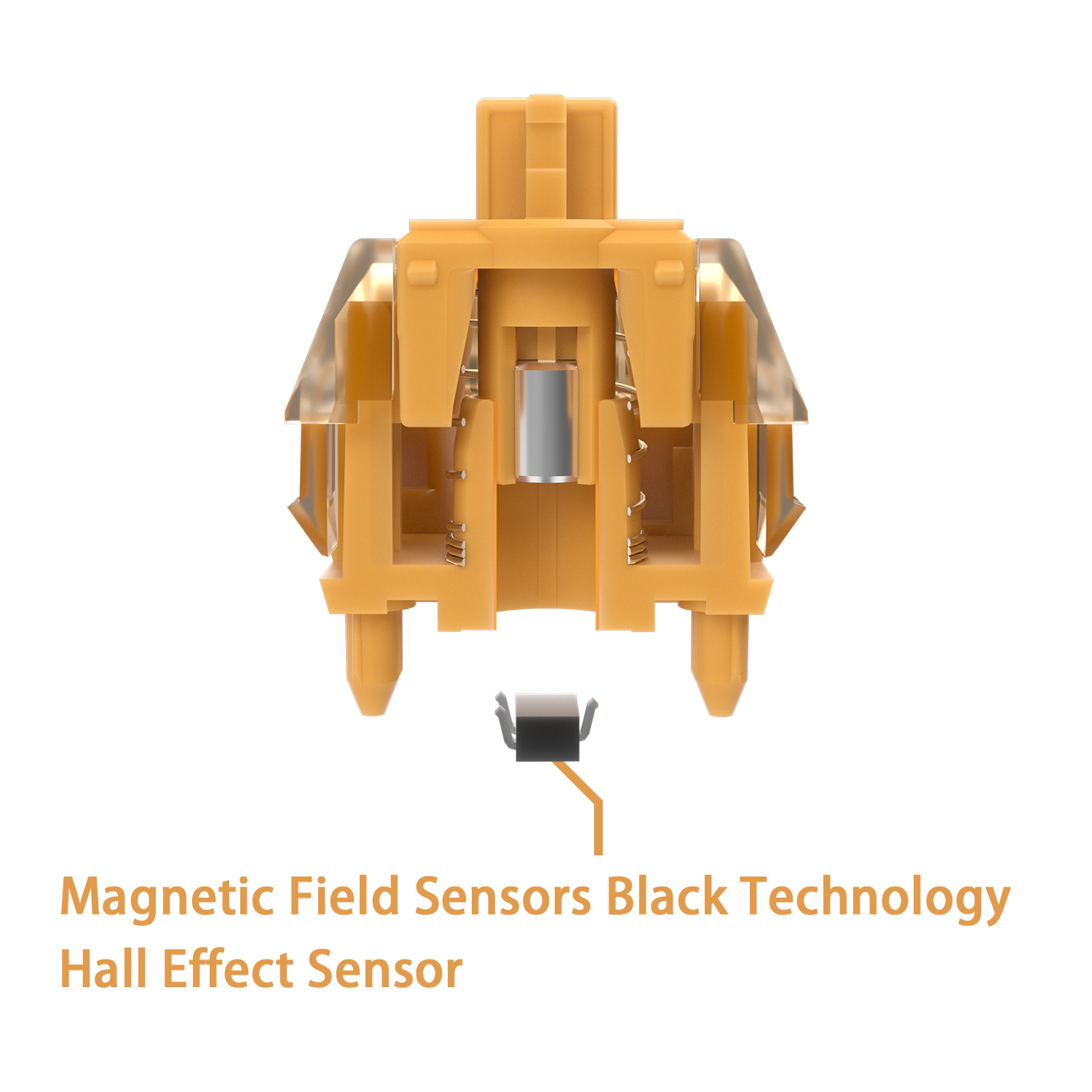
As it is obvious that switches of these three types are incompatible between, optical and electromagnetic sometimes are incompatible even in class. For optical type, the construction and location of the light path can vary a bit. For electromagnetic type, the biggest problem is the polarity of the magnet. So pay attention to it and do the research.
Mounting
Considering that mechanical switches with electrical signal type are literally just a self-sufficient electrical component with two metal pins, they can be pre-soldered on the board like any other electrical component. And this is how it was years ago. Now days, for the sake of fast and non-destructive customization, almost all custom keyboards are hot-swappable. In this case, special hot-swappable connectors are pre-soldered to the board and work like normal spring-loaded terminals into which two metal contacts are inserted.
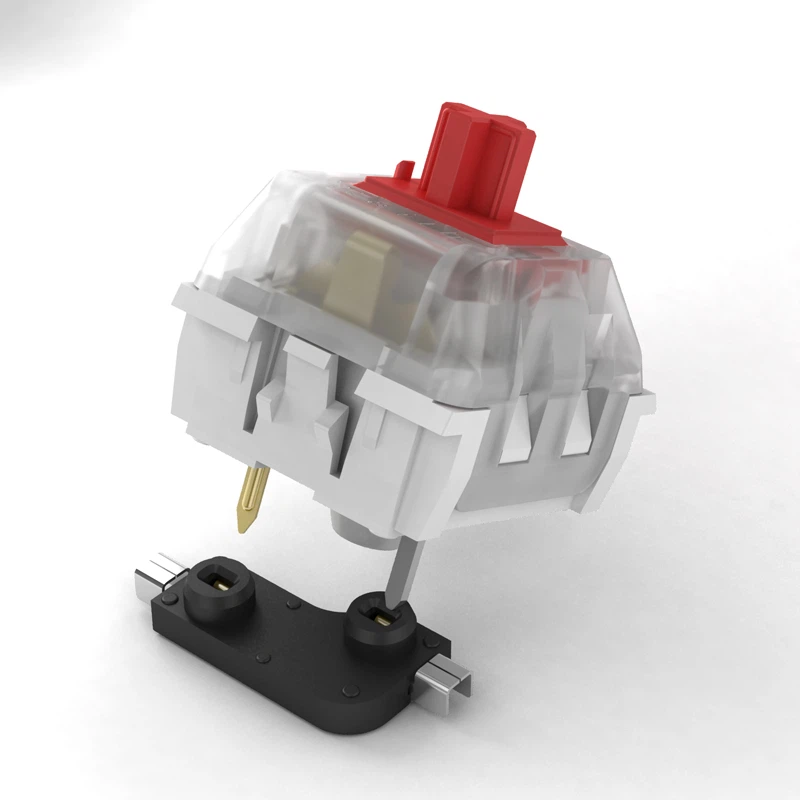
Switches with other signal transferring types are not self-sufficient because they can't operate as switches without additional elements that located on the board. And because there is no direct connection, there are no problems with making such switches hot-swappable, so they are by default.
Basic mechanical switches with electrical signal type usually have a more common 3-pinned design. Center mast bottom part considered as 1, and metal pins from leaves as 2 and 3. Such type of mount is also called "plate-mounted".
But some switches have a 5-pinned design with two additional plastic pins with the sole purpose of providing more stable positioning. These days, more and more mass-market and almost all premium manufacturers are implementing 5-pin mounting sockets. Therefore, compatibility is not an issue in most cases anymore. Such a type of mount is also called "PCB-mounted".
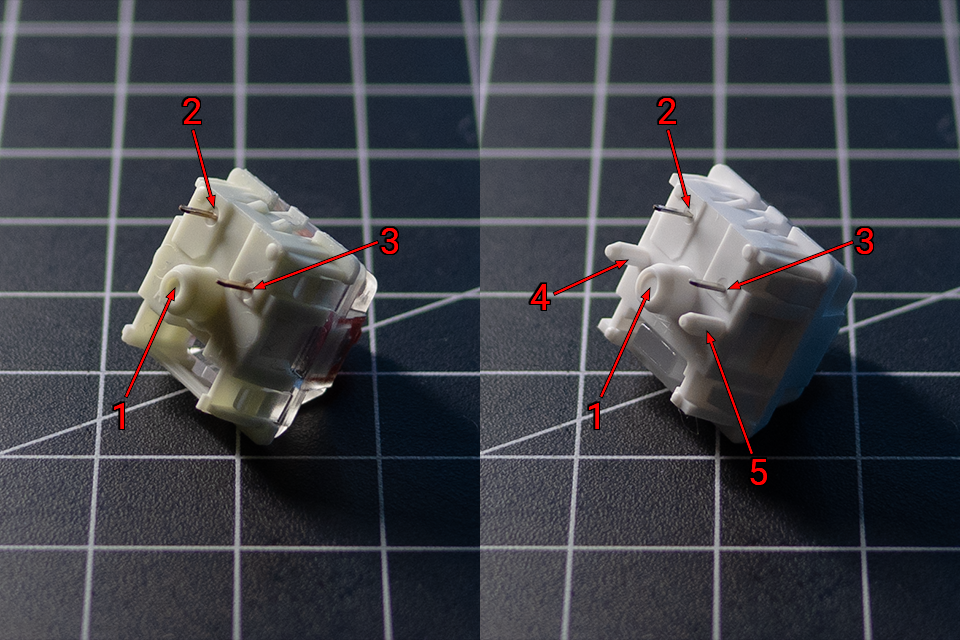
Moving mechanism
Now we are going to examine moving mechanisms inside the switch and if something was not clear until this moment, now it all should fall into place. So, there are three types of moving mechanisms:
Linear
The stem is the only one moving part. The legs of the stem are smooth and have no tactile bump. During transition, the stem glides over dynamic leaf arms with its legs, and because the legs are smooth, there is no tactile presence of any kind.
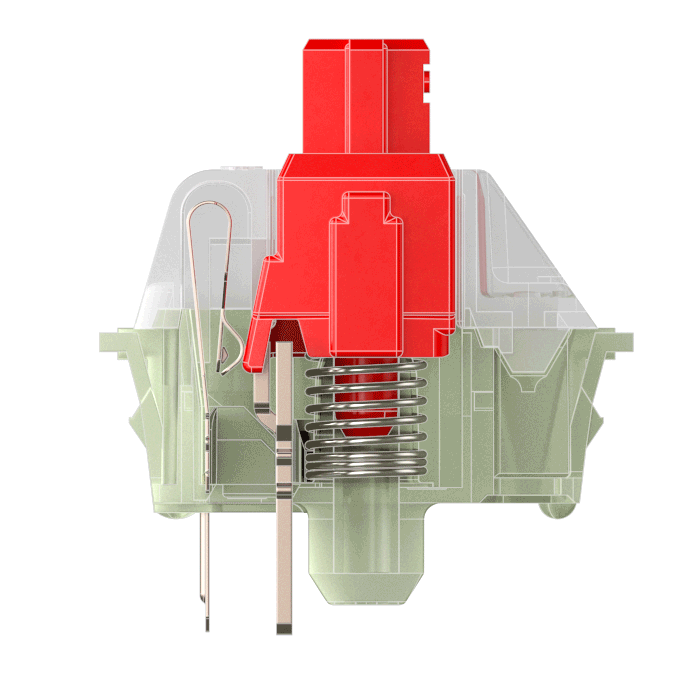
Tactile
The stem is the only one moving part. The legs of the stem have a variation of tactile bumps. During transition, the stem glides over dynamic leaf arms with its legs, and when it overcame a tactile bump, resistance adds a small tactile presence.
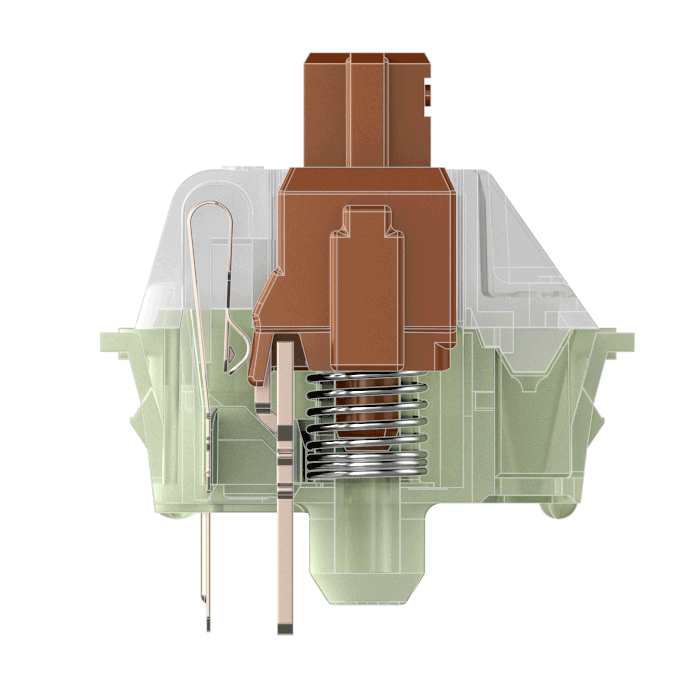
Click
The moving part consists of two elements: stem and click jacket. The legs are located on the click jacket instead of the stem, and bumps on them serve a role of the hooks. From the start of transition, bumps on the click jacket legs clung to dynamic leaf arms, so when the stem goes down, the click jacket stays in place for some time. And when the resistance of the tactile bump is overcome, click jacked hits the bottom with all accumulated force. It adds a distinctive sound and tangible recoil feedback.
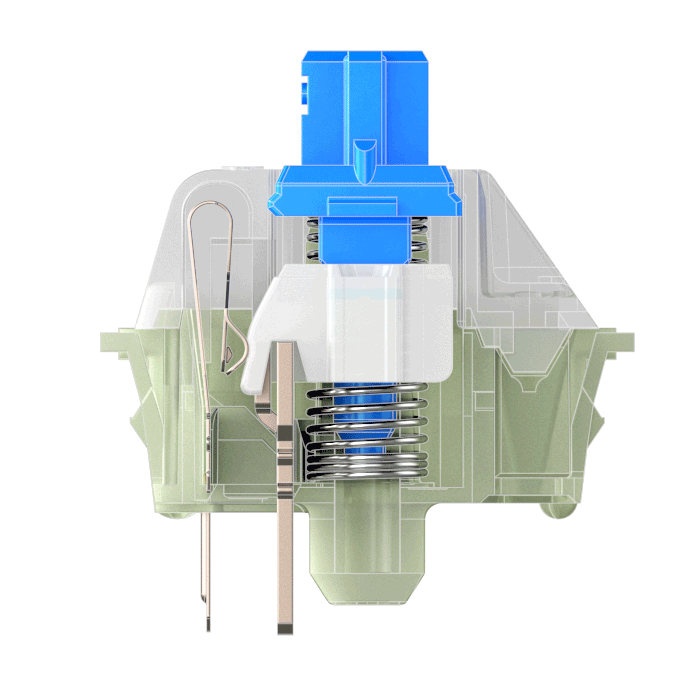
Spring type
From the beginning, the main criteria in spring selection were its weight. Not literally the weight of the spring, but the force in grams you need to apply to compress this spring fully. These criteria define the actuation force of the mechanical switch and have no clear requirements or classification and can therefore be varied between switch models. Typically, springs with fewer turns are made of thicker wire and are therefore stiffer and, as a result, heavier.
After some time, we got another criteria: number of contraction segments.
Standard springs have only one contraction segment. Such springs are usually shorter, so compression preload is low. As a result, when you are pressing it, you can feel exponential resistance buildup. Such springs have more tendency to pinging.
Multi-stage springs have more than one contraction segment. Typically, used 2 and 3 segmented versions. Such springs are longer, so the compression preload is higher. As a result, when you are pressing it, you can feel more linear resistance along the whole path. Static transition segments relieve the spring, make it a bit more balanced, and this reduces the chance of pinging.
Materials
The combination of materials from which the switch parts are made directly affects the tactile and acoustic characteristics, so manufacturers constantly keep experimenting with it. The most common are: polycarbonate, nylon, and POM. But as I mentioned, there are dozens of blends and variations, so it is literally not possible to classify anyhow.
To be continued...
My current config
As a conclusion of all we are taking above, I want to show my current config. For now, I made a big video in my native language where I am assembling a semi-custom mechanical keyboard based on barebone MonsGeek M1 V5 VIA ANSI. In the future, it will be plenty of additional upgrades to it and all this will be represented here. But for now, just a long meditative video of how complete noob assembling keyboard.
Created by TennojiM
All rights reserved
© 2025
All rights reserved
© 2025